HIAMIDE 2010 SERIES – CO-SOLVENT RESINS
The HIMIDE 2010series of resins may be considered as the traditional polyamide ink binder. This range is particularly suited for the production of gravure inks and the resins are characterized by their:
- Excellent resistance to blocking
- Good solvent release
- Poor tolerance to polar solvents
- Poor gelation recovery
HIAMIDE 4030 SERIES – CO-SOLVENT RESINS
The HIMIDE 4030 series of resins may be considered as the traditional polyamide ink binder. This range is particularly suited for the production of gravure inks and the resins are characterized by their:
- Excellent resistance to blocking
- Good solvent release
- Good water resistance
- Poor tolerance to polar solvents
- Poor gelation recovery
HIMIDE 6010 SERIES – ALCOHOL REDUCIBLE RESINS
The HIMIDE 6010 series of resins offer properties intermediate between cosolvent and alcohol soluble resins. The range is suited for the production of both gravure and flexographic inks. Compared to co-solvent resins, these resins have:
- Improved tolerance to polar solventsg
- Improved gelation resistance
- Good blocking resistance
- Improved compatibility with nitrocellulose
HIMIDE 9030 SERIES – ALCOHOL SOLUBLE RESINS
The HIMIDE 9030series of resins offer a wider variety of properties than the cosolvent and alcohol reducible resins. These resins are particularly suitable for the production of flexographic inks but generally require the incorporation of nitrocellulose to optimize performance. The resins offer:
- Excellent tolerance to polar solvents
- Very good compatibility with nitrocellulose
- Poor to good blocking resistance
- Poor to good water resistance
- Low solution viscosities
- High melting points
HIMIDE 1002/H SERIES – ALCOHOL SOLUBLE RESINS
The HIMIDE 1002/H series of resins offer a wider variety of properties than the co-solvent and alcohol reducible resins. These resins are particularly suitable for the production of flexographic inks but generally require the incorporation of nitrocellulose to optimize performance. The resins offer:
- Excellent tolerance to polar solvents
- Excellent compatibility with nitrocellulose
- Very good compatibility with nitrocellulose
- Poor to good blocking resistance
- Poor to good water resistance
- Low solution viscosities
- High melting points
PHYSICAL PROPERTIES AND APPLICATIONS
Grade | Melting Point°C | Soln (1) Viscosity: Sec Ford cup B-4 @ 25°C |
Uses | Features |
---|---|---|---|---|
HIMIDE 2010 | 105 – 115 | 43 – 65 | Gravure Inks and Lacquers |
Excellent Solvent Release |
HIMIDE 4030 | 100 – 110 | 30 – 46 | Gravure Inks and Lacquers |
Improved Solubility |
HIMIDE6010 | 115 – 125 | 19-29 | Gravure &Flexographic Inks and Lacquers |
Good gelation resistance and antiblocking properties |
HIMIDE9030 | 100-110 | 16-24 | Flexographic Inks |
Good water resistance and low odour |
HIMIDE 1002/H | 105-115 | 16-25 | Flexographic Inks |
Good Adhesion on Untreated PP & HDPE. |
Resin 35% n Propanol 65%
INFORMATION SHEET:
HIMIDE 2010
Description
HIMIDE 2010 is a co-solvent thermoplastic polyamide resin designed for use in gravure inks and lacquers. HIMIDE 2010 is the highest viscosity grade of the standard range of HIMIDE non-reactive polyamide resins. The composition of HIMIDE 2010 is similar to that approved under FDA 175.320-“Resinous and polymeric coatings for polyolefin films.
Typical Properties
- Acid Value
- Amine Value
- Softening Point (Ball & Ring)
- Solution Viscosity
- (35% in n-Propanol: Ford cup B-4)
- max 6 mg KOH/g
- max 6 mg KOH/g
- 105 – 115°C
- 43 – 65 seconds @ 25°C
Application
HIMIDE 2010 exhibits the properties of the traditional co-solvent group in resins with poor resistance to gelation and low tolerance to polar solvents but excellent solvent release and good lay. Incorporation of phenolic resin will improve the performance characteristics of the resulting inks or lacquers. For optimum solubility, blends of alcohols and hydrocarbons are recommended.
Packaging
Available in 25 kg bags normally 500 kg per pallet.
Shelf Life
Store under cool, dry conditions, It is recommended that the material be used within 12 months of certification.
Handling
HIMIDE polyamide resins are not classified as dangerous and present little or no toxic hazard at normal ambient temperatures, providing good standards of industrial and personal hygiene are practiced.
However, dust may be produced during handling and the wearing of protective masks and precautions to avoid potential dust explosion etc. are required.
INFORMATION SHEET:
HIMIDE 4030
Description
HIMIDE 4030 is an alcohol reducible thermoplastic resin containing wax for specialist applications.
Typical Properties
- Acid Value
- Amine Value
- Softening Point (Ball & Ring)
- Solution Viscosity
- (35% in n-Propanol: Ford cup B-4)
- max 6 mg KOH/g
- max 6 mg KOH/g
- 100 – 110°C
- 30 – 46seconds @ 25°C
Application
HIMIDE 4030 exhibits good relation resistance and anti blocking characteristics. Alcohol dilutability is excellent with HIMIDE 4030 being border line between the alcohol reducible and alcohol soluble types. HIMIDE 4030 has an extremely low odour making it suitable for inks and lacquers where odour is critical. Co-efficient of friction for lacquers made from this resin are typically 0.31 static; 0.295 dynamic.
Packaging
Available in 25 kg bags normally 500 kg per pallet.
Shelf Life
Store under cool, dry conditions, It is recommended that the material be used within 12 months of certification.
Handling
HIMIDE polyamide resins are not classified as dangerous and present little or no toxic hazard at normal ambient temperatures, providing good standards of industrial and personal hygiene are practiced.
However, dust may be produced during handling and the wearing of protective masks and precautions to avoid potential dust explosion etc. are required.
INFORMATION SHEET:
HIMIDE 6010
Description
HIMIDE 6010 is a medium viscosity alcohol soluble polyamide resin for use in flexo graphic inks and lacquers, where water resistance is less important.
Typical Properties
- Acid Value
- Amine Value
- Softening Point (Ball & Ring)
- Solution Viscosity
- (35% in n-Propanol: Ford cup B-4)
- max 6 mg KOH/g
- max 6 mg KOH/g
- 115 – 125°C
- 19 – 29 seconds @ 25°C
Application
HIMIDE 6010 exhibits good gelation resistance, compatibility with nitrocellulose and low odour. However, the good anti blocking characteristics of HIMIDE 6010 allow its use for inks and overprint lacquers where water resistance is not critical.
Packaging
Available in 25 kg bags normally 500 kg per pallet.
Shelf Life
Store under cool, dry conditions, It is recommended that the material be used within 12 months of certification.
Handling
HIMIDE polyamide resins are not classified as dangerous and present little or no toxic hazard at normal ambient temperatures, providing good standards of industrial and personal hygiene are practiced.
However, dust may be produced during handling and the wearing of protective masks and precautions to avoid potential dust explosion etc. are required.
INFORMATION SHEET:
HIMIDE 9030
Description
HIMIDE 9030 is a co-solvent thermoplastic polyamide resin designed for use in packaging inks and lacquers. Compared to HIMIDE 4030, HIMIDE 9030 has much improved solubility characteristics, compatibility with nitrocellulose and greater tolerance to alcohol and polar solvents.
Typical Properties
- Acid Value
- Amine Value
- Softening Point (Ball & Ring)
- Solution Viscosity
- (35% in n-Propanol: Ford cup B-4)
- max 6 mg KOH/g
- max 6 mg KOH/g
- 100 – 110°C
- 16-24 seconds @ 25°C
Application
HIMIDE 9030 retains the beneficial properties of the traditional co-solvent polyamide resins with the added advantage of improved resistance to gelation and greater tolerance to polar solvents. The compatibility of HIMIDE 9030 with nitrocellulose is much improved to that of other HIMIDE range of products. Incorporation of a phenolic resin will also improve some of the performance characteristics of HIMIDE 9030. For optimum solubility blends of alcohols and hydrocarbons solvents are required.
Packaging
Available in 25 kg bags normally 500 kg per pallet.
Shelf Life
Store under cool, dry conditions, It is recommended that the material be used within 12 months of certification.
Handling
HIMIDE polyamide resins are not classified as dangerous and present little or no toxic hazard at normal ambient temperatures, providing good standards of industrial and personal hygiene are practiced.
However, dust may be produced during handling and the wearing of protective masks and precautions to avoid potential dust explosion etc. are required.
INFORMATION SHEET:
HIMIDE 1002/H
Description
HIMIDE 1002/H is a general purpose low odour alcohol soluble polyamide resin for flexo graphic packaging inks. Optimum performance requires higher levels of nitrocellulose than HIMIDE 9030.
Typical Properties
- Acid Value
- Amine Value
- Softening Point (Ball & Ring)
- Solution Viscosity
- (35% in n-Propanol: Ford cup B-4)
- max 12 mg KOH/g
- max 6 mg HCL/g
- 105 – 115°C
- 16 – 24 seconds @ 25°C
Application
HIMIDE 1002/H has excellent nitrocellulose compatibility and optimum performance of and ink is obtained with relatively high levels of nitrocellulose. The low odour of HIMIDE 1002/H makes it suitable for food packaging inks. HIMIDE 1002/H complements HIMIDE 9030 and between them they span the normally encountered levels of nitrocellulose with HIMIDE 9030 being suitable for lower levels. A solubility characteristic of HIMIDE 1002/H is excellent and is gelation resistance. HIMIDE 1002/H can be considered as a general purpose, alcohol soluble resin for flexographic inks.
Packaging
Available in 25 kg bags normally 500 kg per pallet.
Shelf Life
Store under cool, dry conditions, It is recommended that the material be used within 12 months of certification.
Handling
HIMIDE polyamide resins are not classified as dangerous and present little or no toxic hazard at normal ambient temperatures, providing good standards of industrial and personal hygiene are practiced.
However, dust may be produced during handling and the wearing of protective masks and precautions to avoid potential dust explosion etc. are required.
PROPERTIES OF POLYAMIDE INK RESINS
The properties measured for every development or production resin include those related to the chemistry of resin, and those specific to its performance as on ink.
Knowledge of resin chemistry is essential to obtain reproducibility of molecular weight and other physical parameters. Similarly, a knowledge of those properties related to solution and film behavior is required to ensure that satisfactory ink performance is obtained.
Study of all these properties allows the effect of compositional and process changes on ink performance to be assessed.
All comparisons are made using the resin in unmodified form. For continuity, the modifying resin used is a spirit soluble, 1/8 sec. nitrocellulose, which is compatible with all resins at the level used. It is appreciated that many other type of modifying resin are used depending upon the final properties required.
RESIN
- Physical Properties
- Melting Point
- Melt Viscosity
- Odour
- Colour
- Chemical Properties
- Amine Value
- Acid Value
INK
- Solution Properties
- Viscosity
- Alcohol and Ester Tolerance
- Gelation Resistance
- Overnight Stability
- Film Properties
- Water Resistance
- (Crinkle and Scratch Resistance)
- Solvent release
- Anti Blocking
- Tape Adhesion
- Visual Gloss
Full details of test method are available on request.
TEST METHODS FOR POLYAMIDE RESINS
Softening Point
The softening (or melting) point is measured using the ring and ball method with a heating rate of 5 0C per minute. The result is expressed in °C
Acid Value
The acid value is determined by titration with 0.1N alcoholic potassium hydroxide solution using phenolphthalein indicator. The results expressed in mg KOH/g of resin.
Amine Value
The amine value is determined by titration with 0.1N hydrochloric acid using bromo cresol green indicator. The result is expressed in mg KOH/g of resin.
Colour
The colour is determined on a 35% nvc solution in n-propanol using a comparator. The results are expressed in terms of unit on the Gardner scale.
TEST PROCEDURES FOR ASSESSING INK PROPERTIES
Varnish Properties
The varnish properties are determined on a 35% nvc solution of the test resin in n-propanol. The resin is tested unmodified and modified with 20% of an “alcohol soluble” nitrocellulose resin based on resin solids.
Gel Recovery
The gel recovery temperature is the temperature at which the test resin solution becomes liquid after storage at-12 °C for 16 hours.
Polar Solvent Tolerance
The solvents use for determining the polar tolerance is either industrials methylated spirit or ethyl acetate. The amount of polar solvent required to precipitate the test resin from solution is determined and the tolerance is expressed as a percentage over the original resin solution (i.e.1 part resin solution to 1 part polar solvent is 100% tolerance;1 part resin solution to 1.5 parts polar is 150% tolerance).
Solvent Release
Solvent Release is measured as the relative drying rate of the test solution against a fast drying, high molecular weight co-solvent solution (HIMIDE 831, at 35% nvc in n-propanol). A twin channel grind gauge is used. The result is expressed on an arbitrary scale of 0-10, with the standard expressed as 5.
Anti Blocking
Anti blocking is measured as the degree of adhesion between varnish film(varnish to varnish) stored for 16 hours at 40°C and 90% relative humidity under a 1 kg weight.
Ink Properties
The ink properties are determined on flexo graphic inks made from the resin alone and resin modified with nitrocellulose. The inks are pigmented with phthalocyanine blue at a pigment/binder ratio of 0.36:1
Wet Scratch Resistance
The wet scratch resistance is expressed as the resistance of the film to marring or removal by fingernail after being soaked in water at 25°C for 3 hours.
Wet Crinkle Resistance
The wet crinkle resistance is the number of crinkle to remove or damage the film after soaking in water at 25°C for 3 hours.
RECOMMENDATIONS FOR THE SAFE HANDLING OF POLYAMIDE RESINS
A. PRECAUTIONS
1. General
Solid polyamide resins not normally harmful, but can present a dust hazard.
2. Skin Protection
Not normally harmful.
3. Eye Protection
Avoid contact with eyes. Wear eye protection at all times when handling polyamide resins.
4. Respiratory Protection
Avoid breathing dust. Wear suitable dust make when handling polyamide resins.
5. Protection From Fire and Explosion Hazards
The main hazard is represented by dusting from solid polyamide resins. Avoid sources of ignition and take precautions to avoid build up of static.
Efficient ventilation to minimize dust concentrations is essential.
In the event of fire, suitable extinguishers are foam and dry powder carbon dioxide.
Combustion of the resins may yield toxic by-productions; therefore, fire fighters should wear suitable protective clothing including breathing apparatus.
6. Environmental Considerations
Not normally dangerous for the environment.
RECOMMENDATIONS FOR THE SAFE HANDLING OF POLYAMIDE RESINS
B. FIRST AID
C. STORAGE
Store away from sources of ignition.
D. SPILLADE
Powder spillages should be swept up; avoid causing excessive dust, and placed in closed containers for disposal.
E. DISPOSAL
All wastage must be disposed of in accordance with the requirements of the Pollution Control Act.
N.B. when the above resins are formulated into end productions, due account must be taken of other
constituents of the formulations on their handling hazards.
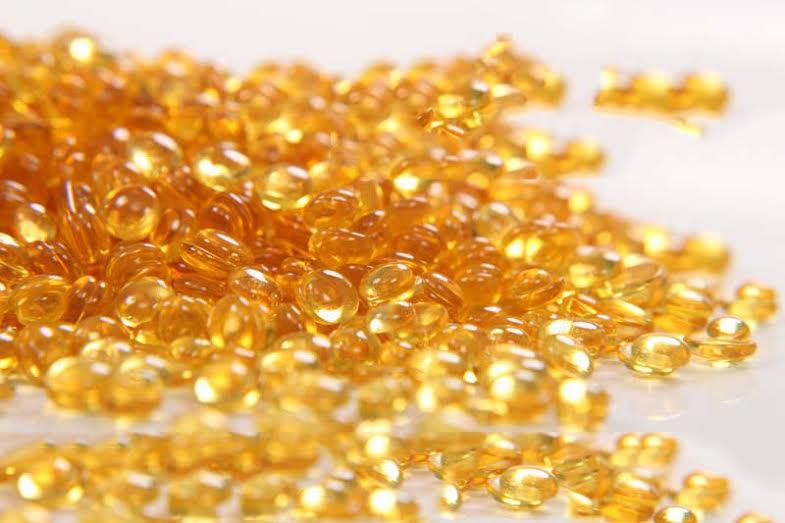